Greenplac is investing on the expansion and verticalization of its the production process, says businessman José Roberto Colnaghi
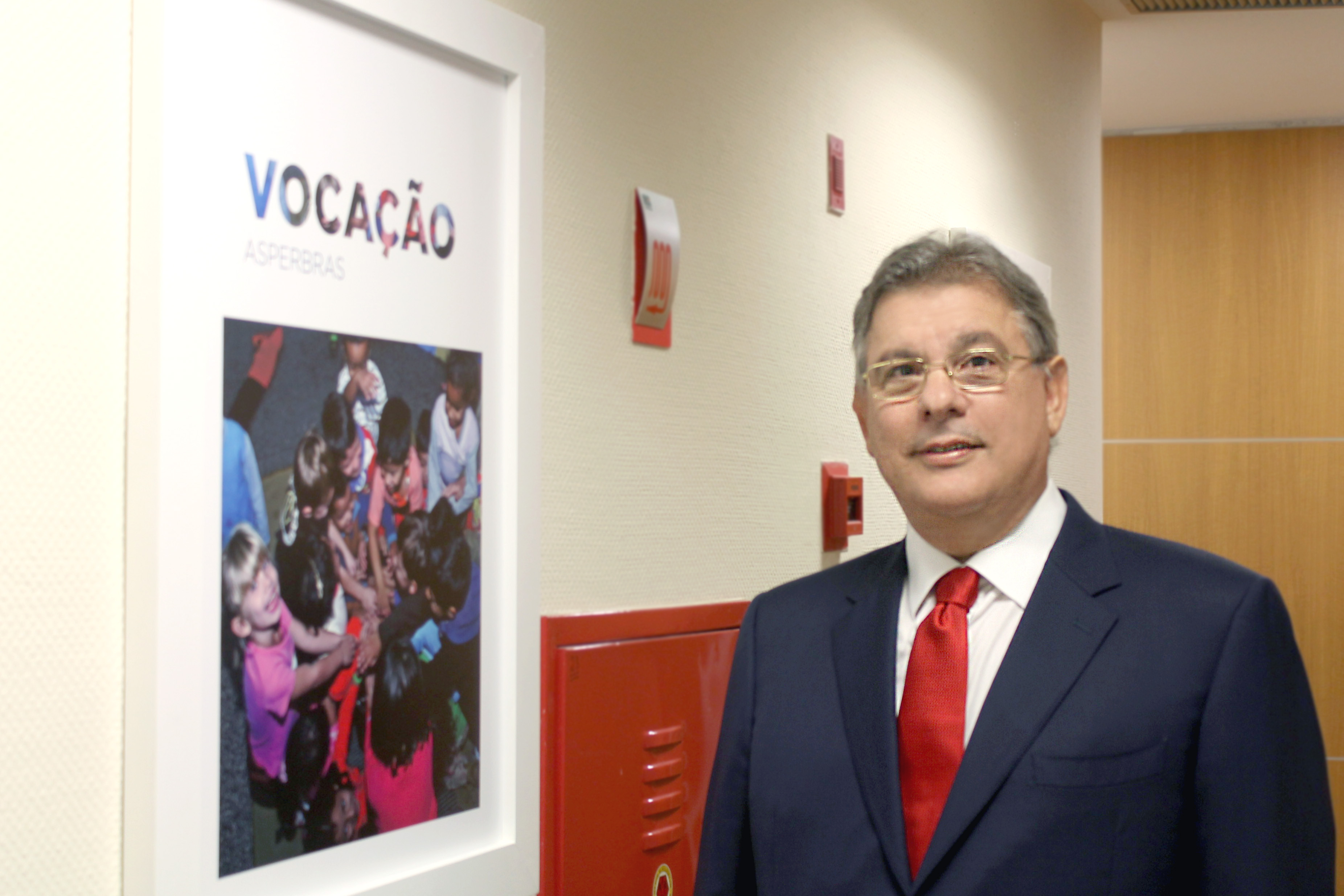
Investments in self-sufficiency in the production of MDF inputs and the search for certifications make the company a benchmark in environmental responsibility, says the José Roberto Colnaghi, president of Asperbras
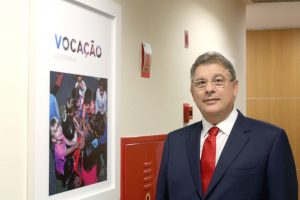
José Roberto Colnaghi, president of Asperbras.
One of the major players among MDF producers in Brazil, Greenplac, a subsidiary of Asperbras, has sought self-sufficiency and sustainability in its production process. After the resin factory started its activities in early 2020, the company is inaugurated the formaldehyde plant, installed in the Greenplac’s industrial complex, in Água Clara (MS). “The new plant will have production capacity to meet Greenplac’s demand and, also, for sale to the foreign market”, says the president of the Board of Directors of Asperbras, José Roberto Colnaghi. “For this reason, we invest in the production of quality inputs, in environmental certifications, modernization of machinery and verticalization of processes, as we know that this directly influences the product offered to the market,” he reinforces.
The result of these investments is one of Greenplac’s greatest achievements – in the year in which the industry completes two years of operation, the company received the recommendation for the FSC – CoC (Chain of Custody) seal. Granted by the Brazilian Council for Forestry Management, the internationally recognized seal identifies responsibly managed forests, capable of reconciling ecological safeguards with social benefits and economic viability.
Verticalization and sustainability
With the new factories, the company continues to verticalize its processes, making Greenplac a producer of 80% of the inputs used in the manufacture of MDF, as it already uses eucalyptus from its own plantations, resin from internal production and water from reuse. The industry’s energy also comes from its own sources – the Guarapuava Thermoelectric Plant, in the countryside of Paraná, is another one of Asperbras’ subsidiaries and indirectly feeds the Greenplac plant through energy compensation.
Recently, the UTE underwent a process of modernization and renovation of its equipment. The necessary tests will take place in the coming months and, thus, will make it possible to reduce the consumption of biomass in the generation of electricity, which may reach its total nominal capacity of 12.3 megawatts per hour.
Considered clean by experts, the energy from biomass linked to the industrial production system ends up making the process even more sustainable, since its combustion returns to nature only the carbon that the plant used to grow.
Business expansion and industrial complex
From reforestation areas to a modern industrial plant, the company has been verticalizing the entire production process, investing in sustainable business and with the latest technology. Following this path, Greenplac expanded its lines with the launch of three new MDF patterns – Freijó Amazonas, Bali and Pietra Bronze.
In addition, it opened a distribution center in Mirassol (SP) – the unit holds about four thousand cubic meters of raw MDF in thicknesses of 2.8mm and 25mm and is an extension of Greenplac in the countryside of São Paulo. The strategic decision came from the company’s board of directors to further improve service to the entire administrative region of São José do Rio Preto.
Seeking to expand the market in which it operates, Greenplac also invested in exportation – the company is finalizing all tests for certification by the CARB (California Air Resources Board) seal, which will enable the export of the brand’s MDF to the United States.
“The possibility of business expansion is the result of Greenplac’s concern with the quality in all its services and products,” says José Roberto Colnaghi.